Tackling Severe Working Conditions: A Case Study On Dry Acetylene Units
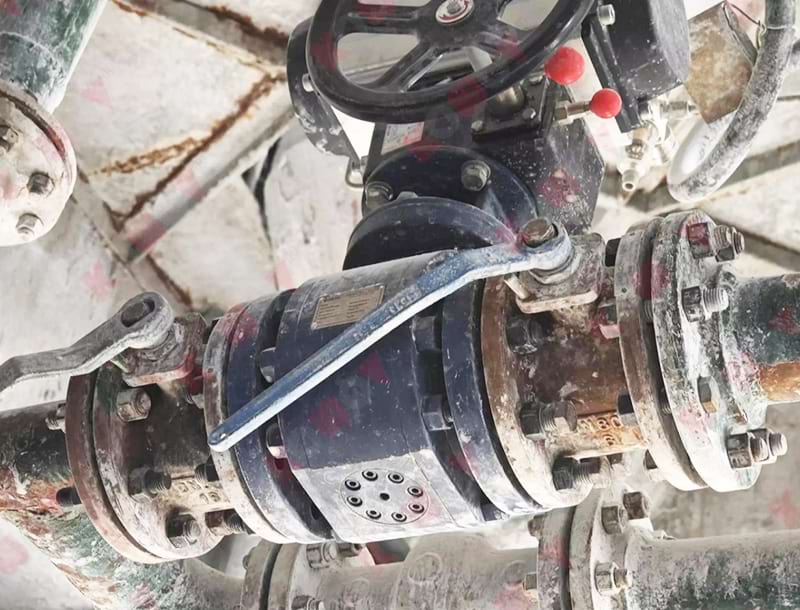
A renowned listed chemical company in China faced severe challenges in its dry acetylene unit, where the scrubber pump outlet liquid level control valve encountered internal leakage issues. As a critical component of the caustic soda production process, the stable operation of the dry acetylene unit directly impacts production efficiency and product quality. Internal valve leakage not only caused material loss and increased energy consumption but also posed safety risks, significantly affecting the company’s productivity and market competitiveness.
The liquid level control valve LV1201 at the scrubber pump outlet handles carbide slag slurry (composed of 4% solid content Ca(OH)₂ solution). The previously used V-type ball valve, with a valve core and seat made of 316+STL, suffered severe wear and tear. This resulted in internal leakage, forcing operators to frequently adjust manual valves to stabilize the scrubber’s liquid level—a labor-intensive and inefficient process.
Introducing the Ceramic C-Valve
Recognizing the harsh working conditions in the acetylene unit, Kingway developed the innovative Ceramic C-Valve in 2017. Designed for challenging applications such as crystallization and clogging, this breakthrough product has delivered exceptional performance over the years, earning widespread market recognition.
In July 2023, after extensive communication and understanding of the customer's pain points, we successfully installed the Ceramic C-Valve at the scrubber pump outlet for precise liquid level control. Since its trial installation, the valve has demonstrated outstanding corrosion and wear resistance, high stability, and consistent performance under harsh conditions. It effectively resolved the long-standing issue of internal leakage and significantly improved liquid level control.
Performance Comparison: Ceramic Valve vs. Traditional Valve
1# Scrubber (Traditional Valve):
· Liquid Level Fluctuations:Large, with a maximum range of 40%.
· Valve Operation:Frequent, with little to no modulation capability.
· Operator Effort: Manual adjustments required every 10 minutes, increasing workload.
2# Scrubber (Ceramic C-Valve):
· Liquid Level Fluctuations: Minimal, with a maximum range of 5%.
· Valve Operation: Smooth and regular adjustments (0–40% range).
· Maintenance: After 15 months, no internal leakage; sensitive and smooth valve action with no signs of scratching or wear on the valve seat or surface.
Monthly liquid level and valve operation curve for the 2# scrubber
Five-minute liquid level and valve operation curve for the 2# scrubber
Long-Term Benefits of the Ceramic C-Valve
The Ceramic C-Valve not only addresses the core operational challenges but also significantly enhances efficiency and reduces maintenance requirements. With its extended lifespan—several times that of traditional 316+STL valves—it offers superior cost-effectiveness in the same price range.
Cost Savings: Reduced valve replacement and maintenance frequency.
Labor Efficiency: Lower manual intervention requirements.
Operational Stability: Safer and more efficient production processes.
Responding to the government’s call for cost reduction and efficiency improvement, this innovative solution aligns perfectly with sustainability goals.
Looking Ahead
Impressed by the valve's performance, the customer has initiated a broader replacement plan, ordering an additional 15 units in August 2024. The Ceramic C-Valve is now undergoing trials in other critical applications such as supernatant liquid handling and carbide slag slurry systems, demonstrating significant potential for further adoption.
This success reflects the customer's trust in the Ceramic C-Valve and heralds a deeper and more extensive collaboration between both parties.
At Kingway, we remain committed to our mission of building harmonious fluid systems through innovative and reliable ceramic valve solutions, tackling even the most demanding industrial challenges head-on. Together, we look forward to creating a future of safe, efficient, and cost-effective operations.
#CeramicValves #FluidControl #IndustrialInnovation #CostEfficiency #DryAcetyleneUnit #SustainableManufacturing #ValveTechnology
Related Blogs
- A renowned listed chemical company in China faced severe challenges in its dry acetylene unit, where the scrubber pump outlet liquid level control valve encountered internal leakage issues. As a critical component of the caustic soda production process, the stable operation of the dry acetylene unit
- A renowned chemical corporation, this client is a pioneer in the petrochemical sector, boasting an impressive global footprint. Based in Shandong, this company became the first in the province to successfully restructure and go public. Its business spans five core areas: polyurethanes, petrochemical